The post No Pressure: How Will JCoP Help Construction Companies Keep Their Water Locked Away? appeared first on UK Construction Blog.
Dan Simmons, Managing Director and founder, Quensus
If insurers were asked to rank what they see as the most costly damages they could incur, you would expect factors like ‘weather’, ‘fire’ and ‘theft’ to sit high up the table. But industry data shows the value of Escape of Water (EoW) claims – i.e. water leaks – is by far greater than anything else claimed.
Despite this risk, however, while a company might have a fire alarm or a burglar alarm, it most likely doesn’t have a ‘water alarm’. And that means it has no way of monitoring its flow of water, and if any leaks have occurred or may occur. To add salt to the water wound, most of the time, leaks are preventable.
On construction sites, the damage caused by the EoW can lead to severe costs – totalling in the hundreds of thousands of pounds (even with insurance in deductibles) – and delays. Without a system that can monitor water flow in real time, sites are highly vulnerable to these risks – and we’ve found that two in every three sites without such a system will report water damages. Clearly, it’s a major problem.

Responding to these challenges, last August the Fire Protection Association, in association with leading industry players, published a new Joint Code of Practice (JCoP) for managing and preventing the EoW on construction sites. The code is an attempt to help “reduce losses associated with EoW events and subsequent project delays”.
But what are the tools companies can use to minimise the risks of EoW?
What the JCoP Means for Construction Companies
The overriding objective of the JCoP is to proactively identify and prevent the risk of water leaks, instead of simply responding to events when they happen. The code dives into many aspects of managing water on construction sites for both pre-construction and construction phases, from plumbing systems and water storage tanks to quality assurance processes. Imperatively, it sets an industry standard for good practice with regards to EoW and water damage prevention.
The JCoP is widely recognised and employed throughout the construction industry and often included in contracts, meaning companies are expected to adhere to its guidelines. By following its measures, construction companies will be able to mitigate costly EoW events and delays.
But to do this, they need to adopt proper water management practices and, crucially, have the tools to do this with. How can they anticipate when an EoW event might occur?
Staying Alert With AI
Managing water usage in real time requires a combination of hardware and software: a system of water sensors, flow meters, valves, and apps. This system enables automatic water flow monitoring and the ability to shut off the supply. How can such a system help construction companies meet JCoP obligations?
Smart valves allow companies to monitor and manage all aspects of water anywhere, anytime. Immediate text and email alerts for leaks enable proactive strategies to automatically shut off water supply out-of-hours or in the event of a serious problem, preventing water damage, high repair and insurance bills, and project disruption.
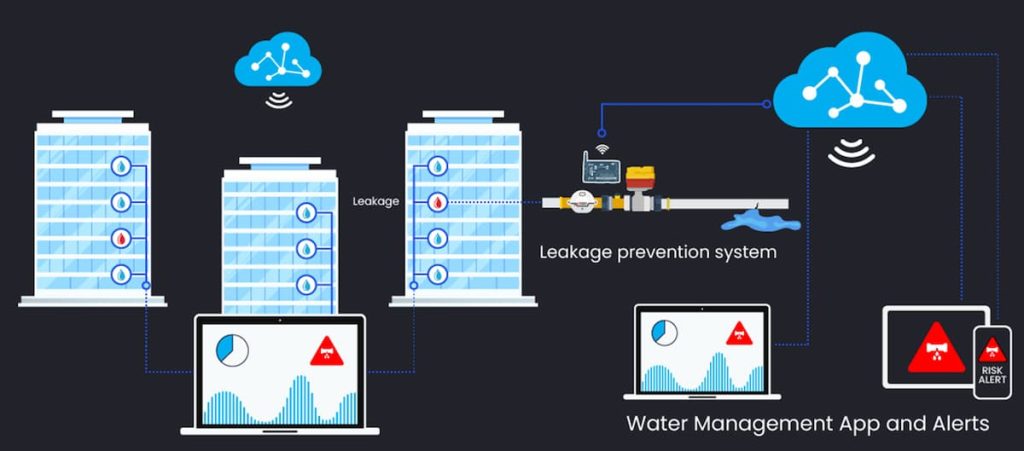
Unlike fire, often simpler to detect, water leaks present a more complex challenge. Leak detection systems use thresholds to trigger alarms or automated actions. There are two main approaches:
- Permanent Thresholds: The traditional method, these trigger alerts based on fixed limits for water flow or volume. However, construction sites have highly variable water usage, making permanent thresholds prone to frequent false alarms. Attempting to avoid these by setting thresholds higher increases the risk of undetected leaks.
- Dynamic Thresholds: The most effective alert systems use dynamic thresholds. These adapt to a site’s specific water usage patterns, varying by time of day and day of the week to create a predictive “envelope” around typical consumption. Advanced platforms employ AI to learn the typical consumption profile for different areas. By analyzing water usage over time (e.g., 1-12 weeks), the system automatically sets optimal leak alert thresholds. Furthermore, potential false alarms (e.g., concrete curing) can be overridden by site personnel, with this information then refining the system’s ongoing learning.
Dynamic thresholds significantly reduce false positives, providing more reliable and actionable leak detection, improving in accuracy and effectiveness with continued use.

Building the Complete Management Plan
Choosing the right water monitoring system is a crucial first step, but a successful outcome demands a comprehensive pre and post-installation management plan. Even the best product is useless without a well-defined strategy for its application. There’s no point installing an expensive burglar alarm on the roof if the user has no idea how to set it! A complete plan integrates product capabilities, installation processes, and ongoing management strategies.
Product considerations should include remote functionality, intelligence (e.g., dynamic thresholds), adaptability, and ease of use. Installation planning involves detailed product specifications, integration with the site’s physical and network infrastructure, installer training, and thorough system configuration. Ongoing management requires user training, establishing and documenting standard operating procedures for responding to leak alerts, and continuous monitoring and record-keeping through a central dashboard.
The success of each component depends on the others, underscoring the need for a collaborative and integrated approach to creating a water management solution tailored to the construction company or site.
Keeping EoW Events Locked Away
The damage caused by EoW events can lead to crippling costs and delays, as well as presenting a significant safety hazard. The JCoP delivers a renewed emphasis for construction companies to assess their water management process and provides industry guidance to help reduce these damages.
Having a leak detection system that can automatically monitor water usage and shut off supply does exactly this. In fact, only one in 10 construction sites using one will suffer damages. Combined with staff training on the principles of the JCoP and effective water management practices on site, construction companies can ease the pressure of managing water leaks events by preventing them in the first place.
And if more take on this approach, we could see ‘water claims’ knocked off the top of the insurer claims table.
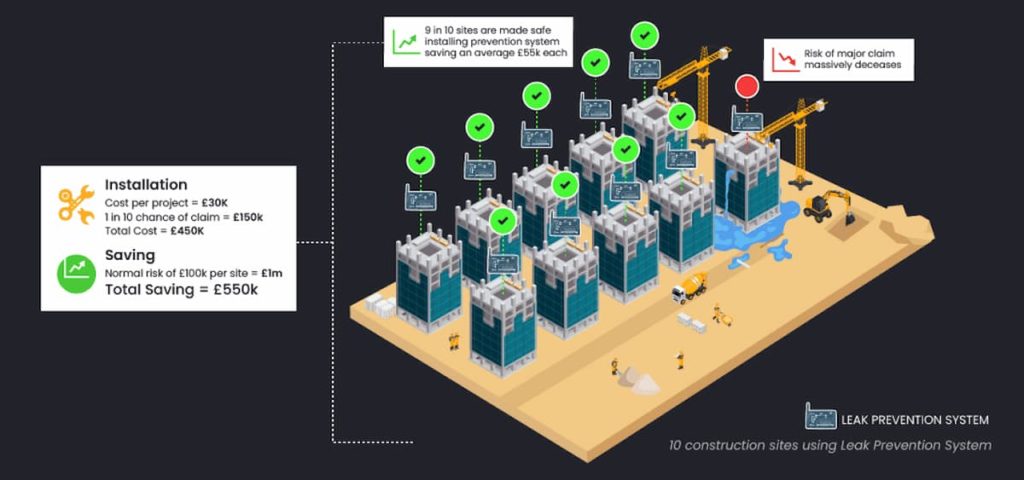