Fire stopping specialist FSi Promat has successfully reduced carbon emissions in a key part of its manufacturing process by 52.5% by switching to a demand responsive system.
The post FSi Promat cuts carbon emissions in key part of manufacturing process by 50% appeared first on Planning, Building & Construction Today.
Fire stopping specialist FSi Promat has successfully reduced carbon emissions in a key part of its manufacturing process by 52.5% by switching to a demand responsive system
By changing the way that a high-pressure air compressor is used at the company’s Measham factory, FSi Promat has reduced the carbon emissions generated through the system by more than half.
A vital part of the production process, the system supplies high pressure compressed air to machinery, used in mixing sealants and coatings.
Installing a variable speed air compressor to replace its existing fixed speed one, means that the system is only using energy when it is actively needed, vastly cutting down the energy that was required for the previous ‘always on’ system.
Switching the machine is one of a number of changes the company has made to support more environmentally efficient operations, including installing a new system to reduce the amount of low-risk wastewater it generates by approximately 550,000 litres a year, moving to sensor-based lighting and using renewable energy.
The manufacturer has also changed shift patterns to support a 30% reduction in energy use by condensing the running time of machinery.
Making an “immediate impact on energy use”
Tim Roe, Engineering and Facilities manager at FSi Promat, said: “Since starting at FSi Promat two years ago I have been looking for ways to improve the energy efficiency of the operation to support the company’s sustainability goals – and those of the wider Etex company.
“This was something I noticed that could make an immediate impact on energy use and that would not have any effect on the manufacturing process at all. The fixed speed air compressor always needed to be on, whether it was being used or not and moving to a variable speed compressor was an obvious choice.
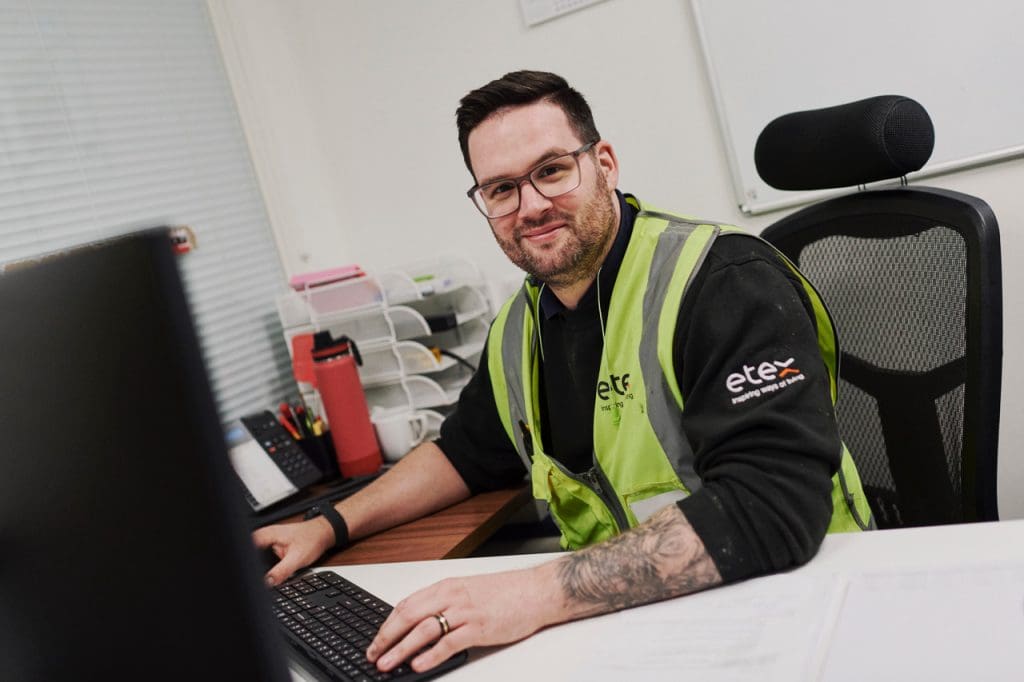
“Installed with minimal disruption, this is a like-for-like switch but due to only being engaged when the compressed air is needed it has seen a considerable reduction in the energy used to power it.
“While safety must remain at the forefront in passive fire protection products, FSi Promat is constantly looking for ways to support more energy efficient operations. Here a relatively simple upgrade has made a considerable impact, and we continue to look for other changes we could make.”
The post FSi Promat cuts carbon emissions in key part of manufacturing process by 50% appeared first on Planning, Building & Construction Today.