BMW said the Spot quadruped from Boston Dynamics works hand in hand with its digital twin technology to help it make sense of its data.
The post How Spot helped BMW address its data blind spots appeared first on The Robot Report.
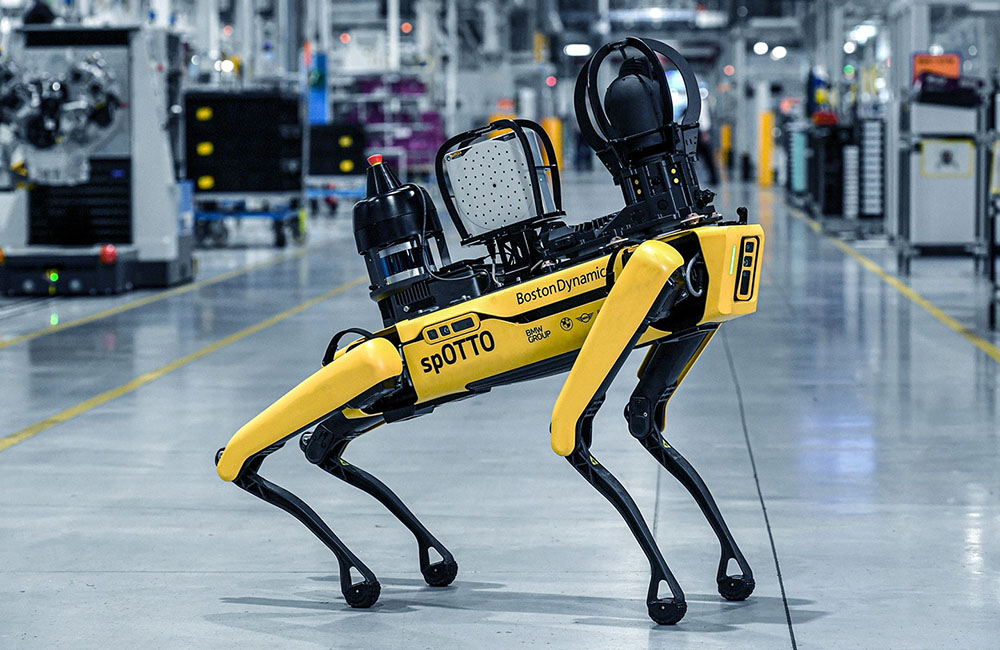
BMW acquired a Spot quadruped from Boston Dynamics to conduct automated inspections in 2023. | Source: Boston Dynamics
BMW Group’s Hams Hall plant near Birmingham, England, generates oceans of data in the process of assembling its engines and components. Making sense of that data, and, more crucially, figuring out where its blind spots are, used to be like sorting through piles of puzzle pieces, according to Boston Dynamics.
Now, with digital twin technology and Boston Dynamics‘ Spot quadruped, the automaker said it’s making the most of the data it generates.
BMW produces engines, data inside Hams Hall plant
The Hams Hall plant machines key engine components and assembles three- and four-cylinder internal combustion engines, as well as V8 and V12 engines, for a range of BMW Group vehicles. Its operating volume production across three machining lines totals 1.4 million components per year, while its two manufacturing facilities produce around 400,000 engines a year.
At one point, internal teams were using over 400 custom dashboards to compile data relevant to their specific areas, all using different methods of data access. Hams Hall needed a “single source of truth” that all team members could access.
In response, the company developed a fully connected digital twin of the facility. Creating the digital twin involved integrating more than 15 IT systems into a three-dimensional model of the factory that team members could access using a smartphone or tablet. The twin now displays live production data using green or red symbols to show the health of a given system inside the factory.
BMW said the amount of machinery required to maintain production is immense, as is the need to ensure that equipment is always working properly via regular inspections. Hams Hall has an extensive tunnel system with pipes, chillers, and hydraulic panels that are vulnerable to air leaks. Despite the critical role of this equipment, the digital twin revealed areas of the facility where inspection data was missing altogether.
It was clear the Innovation and Digitalization (I&D) team needed to assist maintenance workers to expand and automate inspection efforts.
Register today to save 40% on conference passes!
Spot covers inspections
Previously, the factory brought in contractors to inspect for air leaks with specialist equipment. Having the Hams Hall maintenance team take over these manual inspections would take hours away from time spent on actual maintenance or repairs. The I&D team turned to automation instead.
Placing Internet of Things (IoT) sensors on equipment was one option for gathering automated readings, but the I&D team determined it would take years to install all the sensors required and prove too costly. A mobile robot equipped with IoT sensors that could cover the same amount of area, repeating the exact measurements in challenging conditions would be a fraction of the cost. Boston Dynamics’ Spot robot was the clear choice, BMW said.
“We recognized we have a really good level of transparency now in our production data,” said Brad Tomlinson, the technical lead of Hams Hall’s I&D team. “With that transparency, we can start to identify the gaps, and we wanted to use Spot to fill those gaps. We didn’t have temperature data about all our assets, or manual dial readings and acoustic anomaly reports down to specifics. That’s how we’re using Spot.”
Robot makes routine inspections
Spot currently uses several sensors for inspections, including a thermal camera to measure temperature, a Fluke SV600 acoustic sensor to identify air leaks, a 360° camera, and lidar for 3D scanning. As these machines have to be running 24/7, they have priority on auto walks so a schedule is created for a certain station to be inspected once a day, and another station once a week.
For 80% of its schedule, Spot makes routine inspections. However, the other 20% of the time is spent looking forward.
Controlling Spot with a tablet, a BMW team member can bring the robot to production lines for ad hoc inspections. Employees with years of experience and who know their equipment might want to use Spot to investigate a loose bearing or unusual vibration. The intern will bring Spot over to take a measurement, and the team can decide if a repair is urgent or if it can wait.
“It’s almost like completing the loop from Spot to the digital twin and right back down onto the factory floor with the maintenance associates,” said Tomlinson. “Spot’s actually almost fully embedded into the maintenance system.”
BMW quickly gets results with Spot
During the first weeks of inspections with the acoustic sensor, Christian Poss, the Innovation and Digitalization team manager, said Spot found air leaks in unexpected places, which piqued the interest of team members on the factory floor to ensure they were monitored regularly.
Tomlinson says a perfect example of how the legged robot has made operations more efficient is with maintenance requests. Employees can now log into the digital twin, zoom into specific areas to view Spot’s inspection details, and submit a maintenance request right there on screen.
Another clear advantage of Spot is that it doesn’t require years of experience to operate, BMW said. This is especially important because the company has an internship program for university students. In the U.K., undergraduate students dedicate their entire third year of studies to a professional internship.
Interns rotate through every year, however, so BMW Group Plant Hams Hall needed technology interns who could learn and adapt quickly. Spot allows the I&D team to scale inspections and develop other solutions while ensuring a quality internship for students. In fact, two interns lead the Spot integration program.
“We’re working with a team of young professionals, which helps us be agile in terms of how quickly we can roll these things out. Also, it gives these students a really good internship, but it equally reflects on how flexible the existing hardware is.” said Tomlinson.
Register today to save 40% on conference passes!
Boston Dynamics to keynote Robotics Summit
Aaron Saunders, chief technology officer at Boston Dynamics, will give a keynote talk at the Robotics Summit & Expo. The show will be at the Boston Convention and Expo Center from April 30 to May 1. It will bring together over 5,000 developers focused on building robots for a variety of commercial applications.
Saunders will open the second day of the show with a session on “Redesigning Atlas: Boston Dynamics on the Future of Humanoids.”
With over 20 years at Boston Dynamics, Saunders has held key roles, including vice president of engineering. He leads multidisciplinary teams to set the company’s technological vision and align research and development with business needs. Saunders holds a master’s in mechanical engineering from the University of Victoria and a bachelor’s from the University of Alberta.
You can also view the full agenda here to plan your trip and register here. Early bird registration for the Robotics Summit ends Feb. 28. Note that speakers are still being added.
The post How Spot helped BMW address its data blind spots appeared first on The Robot Report.
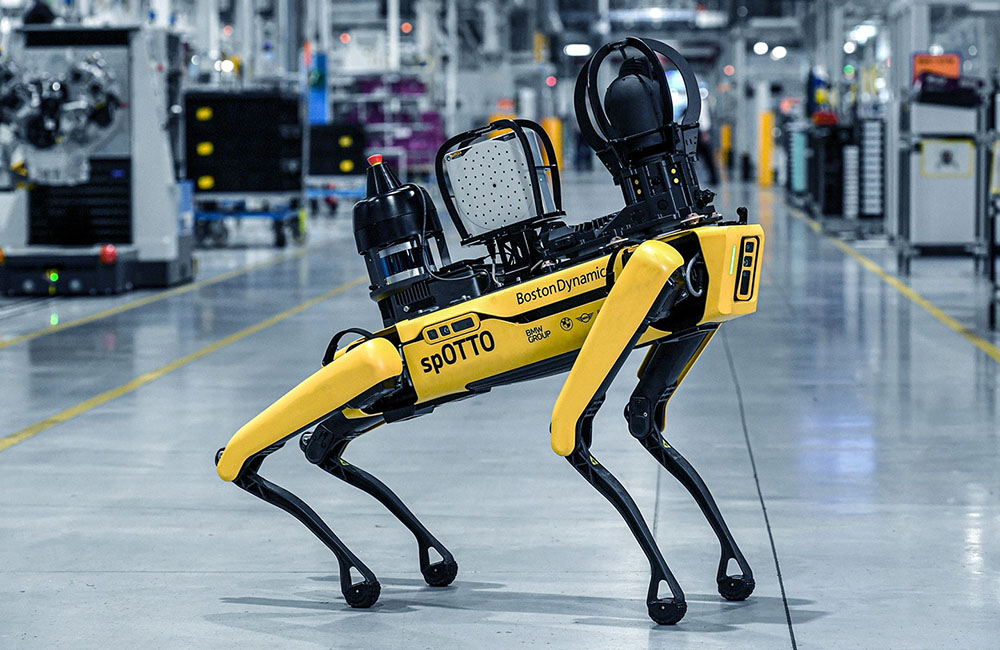
BMW acquired a Spot quadruped from Boston Dynamics to conduct automated inspections in 2023. | Source: Boston Dynamics
BMW Group’s Hams Hall plant near Birmingham, England, generates oceans of data in the process of assembling its engines and components. Making sense of that data, and, more crucially, figuring out where its blind spots are, used to be like sorting through piles of puzzle pieces, according to Boston Dynamics.
Now, with digital twin technology and Boston Dynamics‘ Spot quadruped, the automaker said it’s making the most of the data it generates.
BMW produces engines, data inside Hams Hall plant
The Hams Hall plant machines key engine components and assembles three- and four-cylinder internal combustion engines, as well as V8 and V12 engines, for a range of BMW Group vehicles. Its operating volume production across three machining lines totals 1.4 million components per year, while its two manufacturing facilities produce around 400,000 engines a year.
At one point, internal teams were using over 400 custom dashboards to compile data relevant to their specific areas, all using different methods of data access. Hams Hall needed a “single source of truth” that all team members could access.
In response, the company developed a fully connected digital twin of the facility. Creating the digital twin involved integrating more than 15 IT systems into a three-dimensional model of the factory that team members could access using a smartphone or tablet. The twin now displays live production data using green or red symbols to show the health of a given system inside the factory.
BMW said the amount of machinery required to maintain production is immense, as is the need to ensure that equipment is always working properly via regular inspections. Hams Hall has an extensive tunnel system with pipes, chillers, and hydraulic panels that are vulnerable to air leaks. Despite the critical role of this equipment, the digital twin revealed areas of the facility where inspection data was missing altogether.
It was clear the Innovation and Digitalization (I&D) team needed to assist maintenance workers to expand and automate inspection efforts.
Register today to save 40% on conference passes!
Spot covers inspections
Previously, the factory brought in contractors to inspect for air leaks with specialist equipment. Having the Hams Hall maintenance team take over these manual inspections would take hours away from time spent on actual maintenance or repairs. The I&D team turned to automation instead.
Placing Internet of Things (IoT) sensors on equipment was one option for gathering automated readings, but the I&D team determined it would take years to install all the sensors required and prove too costly. A mobile robot equipped with IoT sensors that could cover the same amount of area, repeating the exact measurements in challenging conditions would be a fraction of the cost. Boston Dynamics’ Spot robot was the clear choice, BMW said.
“We recognized we have a really good level of transparency now in our production data,” said Brad Tomlinson, the technical lead of Hams Hall’s I&D team. “With that transparency, we can start to identify the gaps, and we wanted to use Spot to fill those gaps. We didn’t have temperature data about all our assets, or manual dial readings and acoustic anomaly reports down to specifics. That’s how we’re using Spot.”
Robot makes routine inspections
Spot currently uses several sensors for inspections, including a thermal camera to measure temperature, a Fluke SV600 acoustic sensor to identify air leaks, a 360° camera, and lidar for 3D scanning. As these machines have to be running 24/7, they have priority on auto walks so a schedule is created for a certain station to be inspected once a day, and another station once a week.
For 80% of its schedule, Spot makes routine inspections. However, the other 20% of the time is spent looking forward.
Controlling Spot with a tablet, a BMW team member can bring the robot to production lines for ad hoc inspections. Employees with years of experience and who know their equipment might want to use Spot to investigate a loose bearing or unusual vibration. The intern will bring Spot over to take a measurement, and the team can decide if a repair is urgent or if it can wait.
“It’s almost like completing the loop from Spot to the digital twin and right back down onto the factory floor with the maintenance associates,” said Tomlinson. “Spot’s actually almost fully embedded into the maintenance system.”
BMW quickly gets results with Spot
During the first weeks of inspections with the acoustic sensor, Christian Poss, the Innovation and Digitalization team manager, said Spot found air leaks in unexpected places, which piqued the interest of team members on the factory floor to ensure they were monitored regularly.
Tomlinson says a perfect example of how the legged robot has made operations more efficient is with maintenance requests. Employees can now log into the digital twin, zoom into specific areas to view Spot’s inspection details, and submit a maintenance request right there on screen.
Another clear advantage of Spot is that it doesn’t require years of experience to operate, BMW said. This is especially important because the company has an internship program for university students. In the U.K., undergraduate students dedicate their entire third year of studies to a professional internship.
Interns rotate through every year, however, so BMW Group Plant Hams Hall needed technology interns who could learn and adapt quickly. Spot allows the I&D team to scale inspections and develop other solutions while ensuring a quality internship for students. In fact, two interns lead the Spot integration program.
“We’re working with a team of young professionals, which helps us be agile in terms of how quickly we can roll these things out. Also, it gives these students a really good internship, but it equally reflects on how flexible the existing hardware is.” said Tomlinson.
Register today to save 40% on conference passes!
Boston Dynamics to keynote Robotics Summit
Aaron Saunders, chief technology officer at Boston Dynamics, will give a keynote talk at the Robotics Summit & Expo. The show will be at the Boston Convention and Expo Center from April 30 to May 1. It will bring together over 5,000 developers focused on building robots for a variety of commercial applications.
Saunders will open the second day of the show with a session on “Redesigning Atlas: Boston Dynamics on the Future of Humanoids.”
With over 20 years at Boston Dynamics, Saunders has held key roles, including vice president of engineering. He leads multidisciplinary teams to set the company’s technological vision and align research and development with business needs. Saunders holds a master’s in mechanical engineering from the University of Victoria and a bachelor’s from the University of Alberta.
You can also view the full agenda here to plan your trip and register here. Early bird registration for the Robotics Summit ends Feb. 28. Note that speakers are still being added.
The post How Spot helped BMW address its data blind spots appeared first on The Robot Report.