The post Understanding Types of Cranes appeared first on UK Construction Blog.
Cranes are machines that lift and carry items that are too heavy for people, to places that those people aren’t physically able to carry them.
Types of cranes
Because there are so many industries that have their own requirements and methods of lifting, there needs to be an array of crane styles and categories to cater for them.
There are sixteen main types of cranes. Each of which are unique to specific fields.
Here are some of the most common crane categories that are used in construction:
Tower cranes
There are various types of tower cranes. The main ones used in construction are Self-Erecting Cranes, otherwise known as Pedestrian Operated Tower Cranes (Ped-ops); luffing jibs (luffers), and saddle jibs, otherwise known as flat-tops or saddlebacks. You can learn the difference between luffing jibs and saddle jibs here.
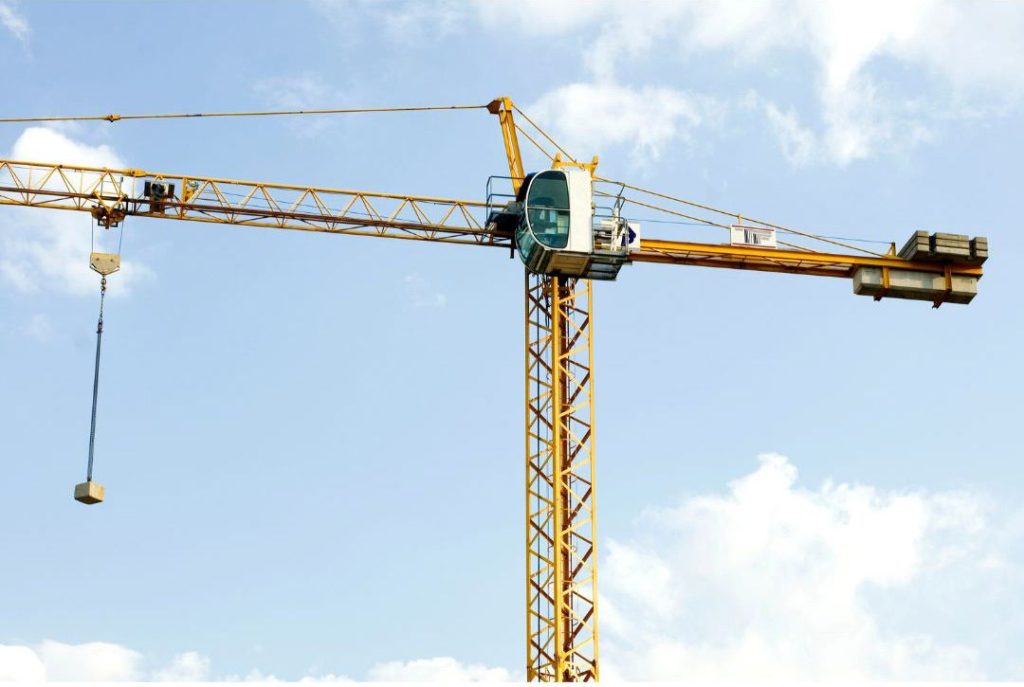
Crawler cranes
Crawler cranes are tracked machines. Some of which are capable of lifting very heavy loads. They generally have lattice booms, of which can accommodate jib extensions if needed. But some have telescopic booms. Crawler cranes get transported to site and built on arrival.
Wheeled telescopic cranes
Wheeled telescopic cranes are more commonly known as mobile cranes. They get driven to site, therefore, operators using them need an HGV license as well as their crane license.
The beauty of mobile cranes is in the name. Because they are so easily transportable, they can be hired for ad hoc lifts, not only in construction but on busy streets, by companies or for domestic use. They’re also often used on wind farms.
How do cranes work?
First, for cranes to work, they need a power source, whether it’s electricity from generators or the main grid, or diesel. Some cranes are now even battery powered.
Cranes work using the age-old system of pulleys and counterbalancing. Steel cable, that is wrapped around a drum attached to a winch, travels through a series of pulleys and sheeves to help increase the lifting capacity. The more pulleys there are, the more weight the crane can lift.
Counterweights at the back of cranes counteract the weight that gets lifted at the front. This helps to prevent the crane from tipping over.

Parts of a crane
Crane parts vary, depending on the type of crane. But the main parts are as follows.
- Hook
- Slew ring
- Boom/jib
- Counterweight
Hook
Crane hooks hang from jibs/booms using hoist rope. Loads and lifting accessories attach to the hooks for lifting.

Slew ring
Crane slew rings are the central part of cranes that help them rotate 360°. They’re also known as turntables.
Counterweight
As stated previously, to keep cranes stable, counterweights at the back counteract weight being lifted at the front. The weight of the counterweights should be greater than the crane’s lifting capacity. Because of this and built in sensors, when cranes do tip over it is usually down to operator error. Cranes that travel on the ground are more likely to tip over than tower cranes, because most tower cranes are anchored into the ground using large bases.
How are tower cranes built?
To most people, quite how tower cranes spring up in city skylines is quite the mystery. Well, it takes a lot of planning, logistics, and teamwork.
The process to building tower cranes goes in these stages:
- Planning
- Base build
- Erecting crane
- Test and sign off
Planning
Engineers, operation managers, and appointed persons (APs) decide what size cranes are going in which locations. The weights of the heaviest loads throughout the project must be predetermined to ensure each crane is sufficient enough to lift them. Also, each crane must have enough reach to cover the majority of the project.
In some cases, various authorities must be notified when a crane is to be erected, such as Network Rail (if the crane will be close to a rail line) and the Civil Aviation Authority (CAA).
The crane must be high enough to clear the structure that it’s due to build. And if it is due to be 100m Above Ground Level (AGL), the CAA must be notified. They must also be notified if crane is to be erected within 6km of aerodromes or airfields, and 10m AGL or surrounding trees or structures, if higher.
Base build
Crane bases are designed and built in relation to elements like ground or existing platform conditions, crane type and size, and local wind speeds.
The types of bases for tower cranes are:
- Piled-foundation bases
- Gravity bases
- Grillages
- Ballasted cruciform bases
This article provides you with a thorough understanding of crane bases.
Erecting the crane
Tower cranes get erected by specialist teams of crane erectors, usually over weekends when sites are not busy, and road closures, if needed, are more attainable. Mobile cranes or other tower cranes are used to lift the crane parts.
Erection procedures and the order of these procedures vary depending on the teams carrying out the work, as well as crane manufacturer guidelines. But here is a simple breakdown of the general erection process.
- Once the crane base is built, a tower section gets anchored to the base. Then other tower sections are added and bolted on top each other until the desired height is reached.
- For extra stability, if a crane is to go too high to be freestanding, tie bars connect the mast to a structure. These get installed at certain intervals.
- If a crane is to eventually be climbed higher to match the full building height, a climbing frame is sometimes installed ready. But this can also be done at a later date.
- A slew ring gets bolted to the top of the tower. This allows the crane to rotate 360 degrees.
- The crane operator’s cab gets attached.
- The counter-jib (or back-jib) gets installed.
- If not preinstalled, winches and electrical panels are placed on the back-jib.
- The main jib gets attached to the front. This is where the crane’s lifting work gets done.
- Ballast weights (counterweights) get installed at the rear to balance the crane out.
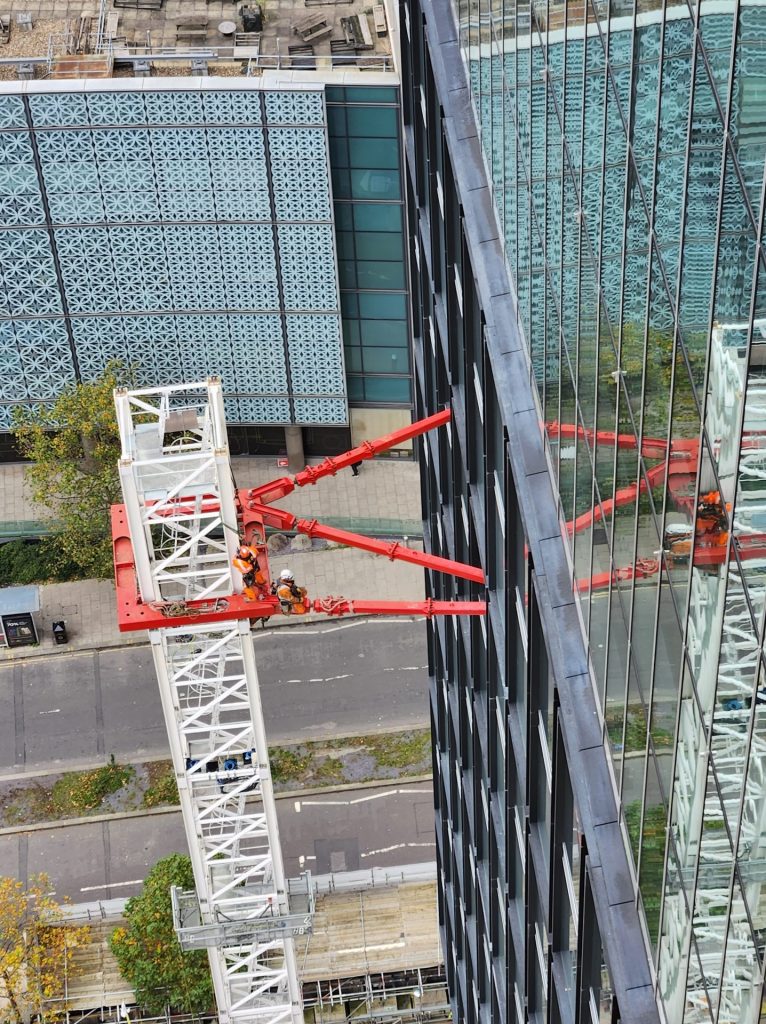
Test and sign off
Once a tower crane is built, all the functions get tested to make sure it is fully operational. Then, the crane lifts a test weight to calibrate the scales and ensure it can lift to its full capacity.
Before the crane can be put to work, it must undergo a LOLER thorough inspection. This gets done prior to use on any lifting machinery assembled on site. This inspection gets repeated annually to certify the crane.